何だカンだと文句を言っていても、時間は無情に(辛!)進みます。(最近、時間経過がやたら速い!・・・年寄りか?・・!)
とり合えず?難問は後回しにして、「大阪城外堀・埋没作戦」? 開始!
|
<機械要素の超・集積体> HONDA S600
ほんの一瞬・えっ?・・ミニカー?・と観たがう光景です。(ウルウル!)
コレに?騙されるんだよなぁ〜!(深く、深く、のめり込んでしまう!)
|
|
「手羽先等一式を外す際、スペアタイヤハウスが邪魔」「デフのフランジのカップリングや上下のデフマウントゴムの問題」で
リフトやミッションジャッキ等を使わない環境下では、体力的エネルギー!が・・・。(年齢的、体力的問題なんですが・・。)
この為、左右の手羽先外側を事前分解しました。
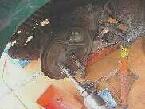 |
ハブとブレーキのバックプレートを先に外して、
手羽先本体の調理すると、安全・迅速に作業できました。
|
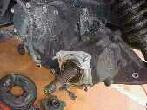 |
|
この部分、本来、グリスのみの給油のはずですが、
右の様に、タラ〜リ・・と、オイルが流れ出てくるケースが・・・。
|
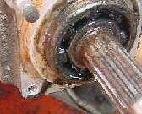 |
|
コレより一気に手羽先内部域作業に突入!しますが、
数々の失敗?から、4点ほど注意する点を学習しました。(こんな私に“学習機能”があるのか?)
1)手羽先分解前にサイドワイヤーを外してフレーム前方に待避します。
|
|
ワイヤーを着けたまま分解すると、ショックを外した時に負担になり、
取付部が欠けてしまいます。
又、フレーム前方にワイヤーを待避しないと、
同じく、ショックを外した際に、フレームと手羽先の間にサイドワイヤーが噛込み、
損傷したり、戻りが悪くなってブレーキの引きずりを誘発します。
|
2)ケースを二つ割する際に「妙に強固にくっついてる!」と思ったら、以下のボルトを再確認します。
|
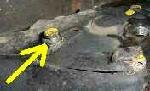 |
チェーン張り用のアームボルトですが、ケース中央で左右の接合に使われています。
特殊環境(水没等)でない限り、無反動ハンマー等でコンコンしていると、
パコッと隙間ができます!
|
錆び付いた位置決めのカラー付近を携帯バーナー等で加熱し、コンコン・・を再開します。
 |
手羽先の更に手羽先部分?のカラーが、
障害になる場合も・・・。
|
|
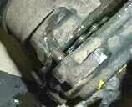 |
40年の前の部品なんだから、気長なペースで作業しましょう!(自己反省!?)
アルミの角が無くなるくらい、強打すると、
最後には、「修理するぞ!」の気合が・・強く凹んでしまう!
(諸事情から、気持ちが凹んだまま、諦めた!なぁ〜・・S600関連は・・。)
|
|
|
|
次はイライラの老舗?デファレンシャルの分解整備開始です。!
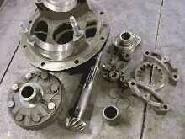 |
まずギアの状態の良いデフを選出して、それを基準に作業を進めます。
小規模でも歯欠け、焼きいれ表面の剥離、歯面のひどい磨耗・・ect・・
・・がある物は、避けます。
当たり前に?歯当たり、プレロード等の調整する事で、「修理直後に破損」なんて事も・・。
新品のギアセットがあれば、とっても楽!なんですが・・・。
|
40年の月日は、決して手羽先を “甘ぁ〜い味付け” にゃ〜?してくれません!
ぴりぴり辛くて、偏頭痛?の連続!
|
ド・レ・ニ・シ・ヨ・ウ・カ・ナ・?
カ・ミ・サ・マ・ノ・イ・ウ・ト・オ・リ・!
・・・なんてノリで、作業が出来たら、楽しい作業?
|
|
|
|
今回、奇跡的か、偶発的(小嬉・笑)か、
想定される消耗部品が、かなり?揃いました。
 |
今回、デフ関係のベアリングは純正部品、及び純正規格品が無い!
ので、すべて社外・代用規格品です。
|
|
今回、当方在庫も合わせて
手羽先・肩部分のシール類が全数、揃った!のは奇跡!
Inter Netの威力・・は今更ながら、ビックリ!
(何でも、当時のS関係の一部の業者さんが、一時期まとめて作製した?)
昭和55年頃、私のS600は、この部分の1種類のシールが欠品で、
高額な単品製作で入手。2個でウン万円!月収の1/3(涙・大粒)
|
|
|
|
今回選択したデフは、ピニオンのガタが全く無いので、実は、疑って?いました。
分解してみると、各ベアリングの磨耗が少なく、ベアリング交換の形跡があります。
と言っても、交換後、部品取りとして放置された期間が長い様で、
水分が溜まってできる腐食痕が各所にあります。
「こちらが下向きで数十年・・・。」の痕跡。
|
新品ギアセットが無い現状では、
恵まれている!と思って作業続行です!
|
|
|
ベアリングのボール部を損傷しない様に
いろんな治具を選んで慎重にピニオンベアリングを交換します。
ボールに直接圧力をかけて傷つけたり、潰したりは、絶対禁止行為です。
(日本男子なら?乱暴には作業できない?ハズだ!)
こりゃぁ〜繊細な男の、繊細な仕事!・・間違い無い!
|
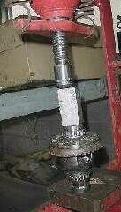 |
|
|
ハイポイドギアには、噛み合う際の接触面を下映像の様に、上下左右を中央付近に調整する、歯当たり調整が必要です。
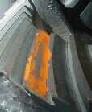 |
走行距離の多いS600でギアセット・再使用!の作業は
かなりイライラ?です!(うまくいかないんです、実際は!)
|
・・・と言うより、この作業、実際は何処で妥協?するか、・・のキビシイ選択なんです!
調整用シム (ピニオン背面に組込)
|
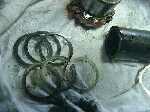 |
この歯当たり調整・・・・デフの騒音と、耐久性に影響大!
|
マニュアルに拠ると、シム選択用の特殊工具があり、厚さを選択する!方式ですが、新品ギアの場合は有効ですが、
旧年式のデフで、再使用の場合は、目安程度にしか?なりません!(とりあえず歯当たりを優先するのが得策です。)
トヨタの場合この特殊工具をマスターゲージと呼びます。
申し訳ないのですが、この後工具や作業用語をトヨタ名称で進行します!
TOYOTA教育を受けた人間=呼称が頭から抜けません!(謝・石頭!)
TOYOTAの場合、サイドベアリング下端にピニオン先端を一致させる様式ですが、
ホンダS600は、サイドベアリング中央より67mmが基本位置?
コレにギアの加工差等を補正する調整作業です。
理論的な精度はホンダ方式!・・が、トヨタ方式が解り易いし、作業性も高い!と思います。
(この考え方の差は当時のメーカー方針の差?)
|
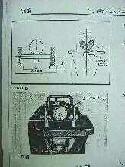 |
トヨタの専門学校(もう約30年前!)の講師の冗談話の一例です。
「技術の日産・サービスのトヨタ!」
「日産の車は技術が優秀だから、パワフルで且つ壊れないから修理の必要性は低い。」
対して、トヨタ車は、
「修理を繰り返しながらも、永く使って戴く設計なんだ!ガンバレ、自分達の仕事は有るんだ。」
わかった様な、わからない様な?話ですが、バブル崩壊を経ての日産、トヨタの現状は、
この冗談話、妙な現実味を感じるのは、私の思い込み?
さらに、レース参戦経験がある、その講師は、
排気ガス規制適合車のスカイラインやフェアレディに対し(名指しではないけど・・)
「名ばかりのGTは道をあける!」のトヨタのCMコピーをひどく皮肉っていました。
「サニーのOHVのエンジンに燃料噴射・DOHCで勝負のメーカーだから(苦笑)・・!」
当時サニーとA12の組み合わせは、奇跡的な程に、全ての面でバランス良く、
スターレットや、レビンがライバル・・・とはとても言えない程の差を感じました。
反面、当時の規制に対して、他社が切り捨てていったスポーツエンジン路線を継続して、
2L、(少し遅れて1,6L)のDOHCを残した戦略は、販売台数の面ではかなり成功した様です。
(・・が、卒業後勤務先で体験した、この時期のエンジン等の修理内容は、・・キビシイ!内容でした。)
「生業としてなら、やっぱりトヨタ系列だな・・。」・・と地元ディーラーに就職した私、
プライベートでは、オートバイで馴染みのある“HONDA”マーク付いた、
N360 や、 life、 S600 に、のめり込んでいく?日々を送りました。
|
|
|
|
|
HONDA S600の場合、
前側のベアリングとピニオンの勘合が甘い!のと、
後側がローラーベアリングの為、トヨタ、日産のテーパータイプに比べ、
はるかに?安易にシムの交換作業が可能です。(プレスを使わなくても可能。)
|
|
歯当たりを見るのに、デフキャリアーの組み付けとバックラッシュ調整が
その都度必要ですので、関係する部分の環境整備?を実施!します。
サイドベアリング接触面に異物の噛込の痕があります。
凹んだ部分の周りが持ち上がるので、手触りを頼りに?修正。
|
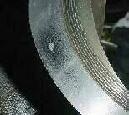 |
|
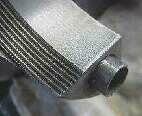 |
サイドベアリングの接触する面の清掃と、エッジ部分を少し修正。
(分解整備歴がある場合、エッジが立って真円度に影響が出る場合があるからです!)
|
|
右のスタッドボルトは、締め付けトルク・6〜7kgcm・・が指定。
ですが・・1600ccクラスの小型デフ(トヨタ)で
12mm程度のこの位置のボルトが、7〜9kgcmです。
この8mmのスタッドボルトが耐えられるとは思えません。
|
実際に、2本ねじ切れました!
(過去にも!)
|
田舎工場整備基準値は、3〜3,5kg−cmが限界!としました。 ⇒
|
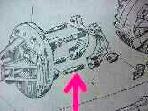
(いい加減な数値で、参考には??)
|
|
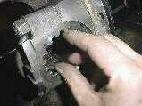 |
サイドベアリング調整用アジャストナットを
ベアリングキャップを軽く締め付け後、
簡単に回せる程度まで修正します。
|
調整ナットのねじ部に薄い影・・が・・。
|
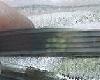 |
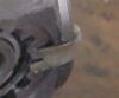 |
ロック取り付け6mmボルトを、ワッシャなし!で組んだ?
|
原始的ですが、スレッド面をヤスリやワイヤーブラシで修正します。 →
|
確実に・・・?
いじけて?しまいそうです!
|
このあたりで、視力、気力が、急激に?低下してきました。
本日閉店です。
(田舎の夜は早い!)
|
 |
一夜明け、気合!が戻った?ところで作業再開です!
TOYOTAでは、ギアの接触面の当たり具合を以下の様に表現します。(他社呼称は判りません!)
|
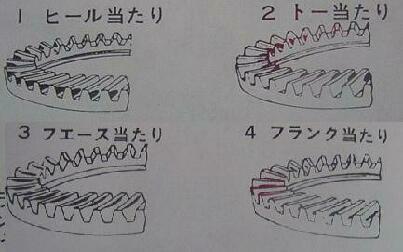 |
イメージ的には?
1)ピニオンのつま先が当る! |
(トー)
|
2)かかとが当たる! |
(ヒール)
|
・・です!
|
そしてリングギアの・・・
3)上っ面が当たる! |
(フェース) |
4)奥深くかみ合う! |
(フランク)
|
・・ですが・・・
深い意味合い?は不明です!
|
|
元々のシムは2枚入っていました。(0,50と0,15mm)
この歯面は加速側(凸面)調整前です。 かなり綺麗な? “トー当たり”!
|
|
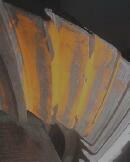 |
0,15mmを抜いた、0,50mmシム厚の減速側(凹面)
トヨタ車は、1ランクのシム減で1/6程度の移動が歯当たり移動の一般的基準です。
このデフでは、1/6よりやや大きめに移動する感じです。(最低シム0,1mm)
ちなみにバックラッシュの変化量もトヨタは、アジャストナット1ノッチで 5/100mm が目安ですが、
このS600のデフでもほぼ近い数値で変移します。(計測上は4/100mm)
|
感覚的に、ピニオンの位置があと0,05mm程度下がれば、“良い感じ”になりそうですが、そんなに薄いシムがありません。
(他社製で調達可能ですが、材質が不明で、この薄さで20kgm近い締め付けトルクに耐えられるか?不安です↓)
今回、旋盤で以下映像のピニオンカラーを削って調整する事にしました。
|
|
田舎工場の旋盤で、5/100mm均一に!は、実は至難の業?です。
最終的には、マイクロメーターの接触感を頼りに?常盤で研磨して仕上げます。
これは、かなりの ストレス蓄積型作業・・です。 歯が浮いてアゴが痛くなります!
最終的には、0,06mm減で完成。
|
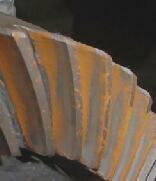 |
減速側最終妥協?位置決定!
大まかな当たりは、中央付近ですが、トー方向にも当たりが残っています。
下映像の加速側歯当たりを見ても判りますが、
ピニオンにある程度前後のガタが出たまま走行していた様です。
|
|
「大阪城外堀埋没作戦・第2期工事」は、ひどく磨耗した ドライブチェーンテンショナー の攻略です!
|
今回、片側しか 新品部品 がありません!
以前、「ローラー部分の交換」
をしているS関係の業者さんがありましたが、現在は・・?
自前でなんとかしなければ・・!
|
|
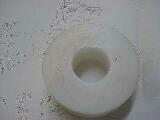 |
この手の部品で良く使う、ジュラコン(POM)を使って複製する事に決定!
一個作って見ましたが、内径の勘合代がなかなか難しく、
数個ボツになってしまい、結局材料から新規購入しました。
どうせ買うなら、素材色を“黒”に!(色で強度や耐久性が変わるとは思えませんが・・・)
|
気持ちの問題?で、黒色の素材から切り出します。
|
|
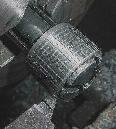 |
真ん中のベアリング外側に滑り止め溝を切り込み、耐衝撃性瞬間接着剤で固定しました。
このサイズでローラーをはめ込む様にすると、
サイドのワッシャーがベアリング外径より大きくなり
将来ローラーが滑る事態発生時、一時的に回避する為です。
|
|
|
|
M6mm でメネジ加工。
|
|
|
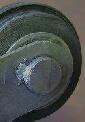 |
一応、軽い圧入ですが、
更に
サイドのプレートに固定。
|
|
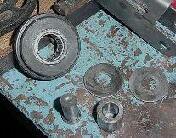 |
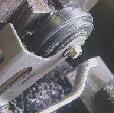 |
ネジロックを塗布して、最終的にワイヤーロック!
カ・ン・セ・イ ・・したぞ!
・・やっと・・(気合抜↓)
今・・何時なんだ?
|
|
|
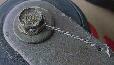 |
作業順が若干前後しますが、
テンショナーシャフト部オイル漏れ対策!
|
|
|
|
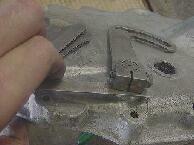 |
この部分の隙間が、結構“あいまい”なんです。
セットボルトのガタがあり、取り付け方次第で、
0〜2mm程度まで変化します。
組み付け後は、このシャフトが引き上げられず、
Оリングの潰し代が無くなり、オイル漏れ発生!
組み付け当初は漏れなくても、
使用過程で、Оリングがヘタって漏れ再発!
以下が、田舎工場の解決策!?
|
|
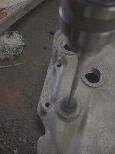 |
シャフト穴をホーニング後、右の様な、“段差”を加工します!
|
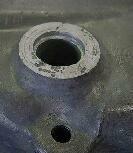 |
|
セレーションシャフト中央に、
M6の雌ネジを切ります。
|
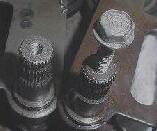 |
今回作製したローラーと同じ材質で、
ツバ付きのブッシュを作製!
|
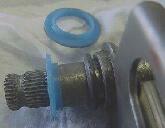 |
|
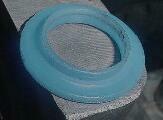 |
|
ツバの厚さをウンウン唸って考え、
シャフトとアームが平面になった時に
適正なつぶれ代に・・・しました!
白色の材料にすれば良かった?(後悔を公開↓)
|
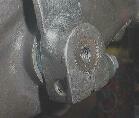 |
|
ワッシャーとM6のボルトで締め付けて完成です!
現在は、水平状態でちょうど良い感じ?にしていますが、Оリングがヘタってきら、
ワッシャー内径を大きくして、中央ボルトを締め付けると、シャフトが持ち上がる!
・・・オマケ付き機構です!(もちろん?後で気が付いた!・・のですが・・・。)
|
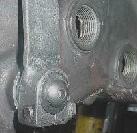 |
|
以前にに1mmφのОリングを入れた経験がありますが、
この部分、チェーンの振動を意外なほど、まじめに受ける?様で、1000km走行程度でOil漏れ再発!
かと言って、ケース内側のサイズ並みのОリングを入れてると、シャフトの受け面積が頼りなくなります。
更にテンショナーのシャフトに種類があって、
今回は、混成部隊?である事も考慮しました。
(多分・・ですが左側が新しいタイプ?)
右のタイプのギザギザを僅かに越える位置まで、ブッシュが届きます。
(ジュラコンは、元々ギアなどに使われていて、こういう部分・用途には、最適?)
|
|
|
本日閉店です。
(田舎の気合は・・弱いし、疲れやすい!)
|
 |
|
かなり疲れきってますが、次回は、
「大阪城 本丸攻略作戦」
手羽先の“皮”?・・に着手・予定。
|
|
いよいよ、本丸決戦!手羽先の“皮”を調理?開始! ここまでの作業なんて、
修理業としては、まだまだ定型作業?(なぐさめの言葉?これって!)
|
|
|
39年式の物は、砂型鋳型で、粗い表面をコーティング処理してあり、
汚れた面を布で拭くと、綺麗な樹脂コーティング面が・・・。
|
テンショナー軸受面には、
樹脂ブッシュが入っています。
砂型の弱点をコストをかけて、
補完してあります。
|
|
|
|
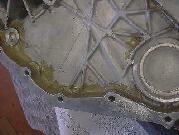 |
40年式以降の型は・・・!
初めて「エポキシ補修」に対面した折の正直な感想は
「なんじゃこりゃ、汚ったねぇ〜!」・・と思ってしまいました。
手羽先の端っこにRKの浮き出し文字があります。
(多分あのチェーンメーカー製?)
|
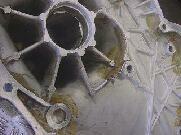 |
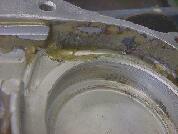 |
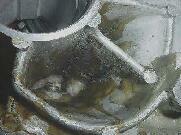 |
|
このリヤスプロケットとネジ穴は、距離が近い為、
ベアリング磨耗や、損傷で、削れてしまう事があります。
(こんなにギリギリでなくても・・と思いますが・・其処はHONDA S600!)
以下はその補修の為のアルゴン溶接時の映像です。
|
|
かなり洗浄したつもりでも、少しの加熱で、下部の鋳型欠損部からオイルの滝が・・!
この滝口が、チーェン調整アームのセットボルトオイル漏れ!の元凶?
|
洗浄後、溶接作業を開始すると、滝の勢いが増します!
|
雌ネジを直し、
美容整形後完成!
|
|
|
|
砂型から、低圧ダイキャストに変更した時期に、発生した鋳型の荒れ部分を細かく拾い上げて、補修している様です。
型を外してその後、切削、穴あけ、ネジ加工した部分に特に注意を払っている様に見えます。
田舎オヤジの勝手な意見なんですが、実際、この処理をしても、手羽先の各部からのオイル漏れは、
完全には止まっていませんし、40年前の過渡期の製品だから・・なんて事も事実、史実?ですが・・・
想像ですが、型抜き後に浸透液で探傷作業後に
「僅かでも可能性のある部分を全部分!出荷前にエポキシ処理した。」のでは?
当時の他社車両部品の実情から比べても、先進的な対応!と思います。
2輪車のクレーム問題で苦闘したホンダの意地?
「ずっと砂型で作れ!」は企業として非現実的で進歩がねぇ〜?
使用者や、オーナーは当時(今も?)ある意味では・・ 「走る実験室」 なのかも知れません。
世界的に高い評価が定着した、 “Made In Japan”
“権利意識とプライド”で造った他国の車より、・・・庶民的で物悲しく、少しだけですが、どこか身近に感じます。
“Made In Japan”・・・“風の中の昴、砂の中の銀河” な? “汗色・涙色の製品”・・・。
|
|
・・なんて身の丈に合わない高いレベルの想像話?はともかく、
直面するオイル漏れを何とかしなければ・・! (そんな物なんだから、そのまま乗れ!・・・実は正論!ですが・・。)
ケース内側に2006年現在の技術で、各種の樹脂コーティング処理も問い合わせしましたが、
ウレタン、エポキシ、フッ素樹脂・・どれを選んでも、ある程度完全な脱脂が条件です。
40年間走り続けたアルミケース内部に浸透したオイルを取り除く事は、不可能?
その上、アルミにプライマー処理をしないと、密着性に問題が有る様で、
この材料としてのアルミプライマーも、イマイチ確立されていない感じです。(温度変化や、オイル漬け環境は無理?)
(ダイキャスト表面も、砂型表面に比べて、離型の兼ね合いで樹脂の密着性は悪い様です。)
当時も“エポキシ処理”しか手が無かった?
|
仮に全面を表面処理すれば、
何でもかんでも限界ギリギリ構造の HONDA・S600!
チェーンの伸びや、調整状態で、ケースに接触は必至!
実際に当たっている!(黄色↓他)
全面処理は無理だ!
|
|
|
田舎の結論・・・・ パンク修理?しかねぇ・・こりゃ!
|
|
エポキシ面の各部がオイルで浮いている反面、コレを完全に取り除く作業は、極みつけ困難です!
サンドブラスト処理も、エポキシを剥ぐより、周りのアルミを削ってしまい問題大!
|
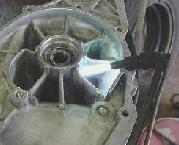 |
本物の調理師のお客さんが、
「玉子焼きを焦がさず焼き上げる方法」を教えてくれた事があります。
「多めの油と強火の火力で一気に焼き上げる!」らしいです。
ぐずぐず、しょ〜たら焦げるがなぁ〜!
|
<翻訳>こういう場合、ゆっくり加熱する方が、
かえって焦げやすいですよ!
|
ケース歪みを最低限に抑える為この強火で一気に!を今回採用しました!
|
温度の目安に周辺のアルミ窪地?に水を張っておきます。
更に歪み対策用に若干外径を落とした(手で簡単に入る程度)捨てベアリングを用意!
アセチレンのバナーで、酸素過剰状態(厚手の鉄を切る程度!)のまま、一気にエポキシ面を焼き切ります。
水滴の状態を見ながら、ガァッと焼いては冷却、再度、ガァッ〜で冷却!を繰り返します。
(一回の時間を出来るだけ短時間で勝負!一気に焼き切ります!)
焼き上がり?です!
いい加減な作業ですが、名付けて?
O2 ブラスト!
sanso?・blast(苦!)
|
|
|
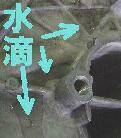
沸騰すると止メ!
100℃軽く?超!
=歪むぞ!
|
水栓?を3個作って・・・ブリーザー部より加圧。
手羽先パンク?点検開始!
|
|
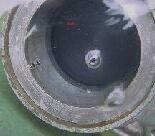 |
一箇所縦線上にポコポコ。
キャップの縁付近の2箇所、
更に加圧すると、4箇所追加!
|
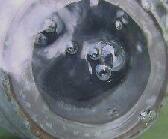 |
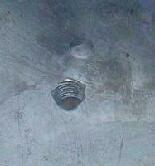 |
手羽先中央のネジ穴も予定通り?
内・外、共に・・ポコポコ。
|
|
この手羽先では、ハブシャフト内部には繋がっていない様です。
ポコポコ無し!
|
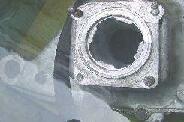 |
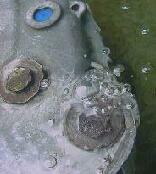 |
ドレンボルト部はボコッボコッ!
ワッシャーや、ボルトに問題なし!ですが
下部のアルミガード部に打痕あり!
取り付け面に歪み有り!
|
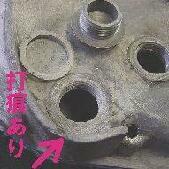 |
|
酸素ブラスト(笑) の前後の映像です。
間違いなく?、エポキシ処理の下には鋳型の荒れや、ヒビ有り。
|
|
 |
想定されるパンク箇所にパンク修理液?を塗りつけて
最近?得意ワザの(苦笑)耐衝撃性瞬間接着剤です!
|
|
事前にパーツクリーナーとエアーガンで、ヒビや荒れ部を洗浄してから、
高圧のエアーで吹き込み、更に同じ作業を数回繰り返します。
(気化した接着剤が鼻や目を刺激します!要注意!)
|
瞬間接着剤は、水分やアルコール成分に反応して固まるらしいので、
水性の洗剤で、洗浄後、パーツクリーナー洗浄そして瞬間接着剤の順番?
・・はかなり有効?・・と信じて?の作業です!
手羽先ドブ漬け点検により、大規模オイル漏れが発生する程の欠陥部分は無かったので、今回は、この方法としました。
大きいクラック等がある場合は、排気ポートののクラックに充填した方法(ミクロの決死圏!?)
・・・の逆圧力方式?でエポキシ充填剤を塗布して、内部加圧して充填処理!
・・・なんて面倒で大袈裟で、気持ちが落ち込む作業が回避!できました(嬉!)
(この場合の様に、通路が狭い=決死圏は?通過が難!って面も考慮しました。)
|
塗布した無駄な接着剤を、その都度、拭取ります。(後々、ハガレ落ちると何かと問題!)
|
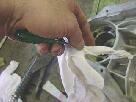 |
この作業の最後に手羽先のブリーダープラグ(息抜き口)を必ず清掃します。
下映像の様に、泥やサビでブリーダーの機能を失っている物が多くあります。
|
|
|
|
“息抜き”がうまく出来ないと、
何事も?問題アリだ!
手羽先内部の圧力が上がって、
オイル漏れ発生!
|
特に内部にゴム製プラグの入ったタイプは要注意!
軟化したゴムとゴミで・・完全封鎖状態発生アリ!
実際はある程度上がるとシールを介してデフ側ブリーダーに逃げるのですが、
このデフ側も同じく詰まり易い!・・・今回デフ側ブリーダー2個の物も発見!
|
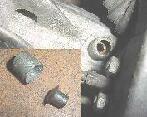 |
本日閉店です。
(田舎の気合は・・弱いし、疲れやすいし、すぐ眠くなる?!)
|
 |
|
|
手羽先調理・最後の仕込み作業です。(やっと・・。)
ちなみにこの部分を 手羽先の肩 ・・と呼びます!
|
手羽先ケースAと、手羽先肩B部・・の磨耗に問題を抱えています。
本来ケースの横方向はサポートの樹脂製のツバをCの面で受けていますが、
手羽先肩の縞状の磨耗が進むと傾いてA部を攻撃?するのかも知れません。
|
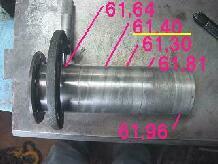 |
5段の径で構成されていて、
黄色線の61,40が、サポートの接触面です。
手羽先との勘合部との間に0,24mmの余裕があるので、
パワーシリンダー等の硬質クロームメッキで、
肉盛りして、サポートの磨耗を補うつもりでしたが、
今回2本、左映像の様な殆ど磨耗の無い物が発掘できました!
|
その差は、手触りでもはっきりわかる程度で、サポートに入れると、
|
縞の位置が合うと
カタカタ・・と、大きく!動きます。
|
|
|
39年式の一回り小さなサポートはこの隙間がかなり小さいですが、
新しい年式になるほど比較的大きめのクリアランスを設定している感じです。(私見です!)
|
|
手羽先・肩は、何故か↓方向が一番磨耗しています。(全数)
多分ですが、加速時や、スタート時の
ピョコンと跳ねる、あの動き!・・が関係している・・
・・と思うのですが頭脳内部で理解!には至っていません(苦笑)
|
|
手羽先・肩は、組替に若干配慮が要りました。
一箇所、穴のピッチが大きいのですが、
各個体で、その寸法が違っている!・・のです。
(数字は穴の内端面距離です。)
|
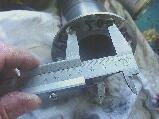 |
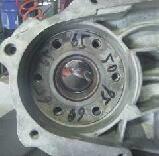 |
年式に拠る差なのか?
取り付けネジの嵌り代を無くす為に
各個体別で加工してあるのか?
|
|
今回の混成部隊方式の部品調達では全く判定不能でしたが、
部品があるのだから、・・文句は言えません!(悲!しかし・・現実↓)
|
色々組み合わせを検討しましたが結局、3つの加工穴に僅かなズレがあり、
取り付けボルトのネジ山保護の為、手羽肩部分に、タップで雌ネジを切りました。
僅かな差なのですが、ボルトを奥まで締め付けた際、締め付けの不安を避ける為です。
|
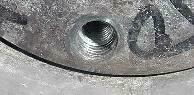 |
|
|
1ヶ月以上の、せつない下積み作業(笑)をやっと終えて、組み付け作業開始!
この一ヶ月間、「まぁ、いいか↓このまま組み付けよう!」・・なんて何度思った事か・・・!
この段階なるとさすがに、落ち込みがちな気持ち↓に俄然、“勢い”が戻ってきます!・・・しかし・・
本日閉店です。
(田舎の気合は・・弱いし、疲れやすいし、すぐ眠くなる・・そして視力が落ちる?!)
|
 |
|
子供の頃、家業が食品関係の小規模な工場で、工場内部の機械のちょっとした修理は祖父の仕事でした。
当時は(昭和30年代後半!)当然の様にその敷地内が、“子供の活動半径の一部”で、
破損したり、磨耗してしまった、やや?手頃な?スプロケット!を発見した私は、伊賀忍者参上!とばかりに、
コレを数個、屋外トイレの壁(木製)へ、シュワッ?シュッ シュッ〜!ドカ ドカ〜 ドカッ!
気持ちは スカッとさわやか! でしたが・・・・ たまたま中に人が↓
|
|
優しかった祖父でしたが、この際のキツイ説教は
“絶対消去不可の大事なデーター”として強制保存されています。
(仮に年老いて記憶が薄らいだとしても・・・!)
|
|
手羽・肩の問題を辛くもクリアし、修理作業に「出口の明かり」が見えてきました。
|
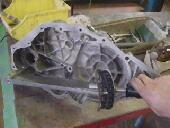 |
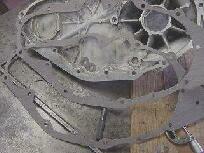 |
今回、スラスト調整の事情で、
G/K厚を0,8から1,0mmに変更しました。
この際同じ厚さで手羽先中央のP/Kも追加作製します。
スプロケットの干渉を避ける為に、
右映像の寸法を現状に合わせて切り詰めていきます。
作業中に脱落し易く、事前に液体パッキンで貼付けます。
|
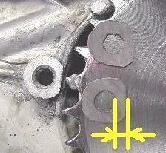 |
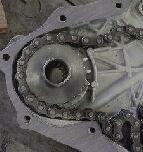 |
とり合えず何でもかんでもギリギリ設計のHONDA S600!
チェーンやスプロケットの干渉を避け作成します。
この辺りはホントにキワドイです!
|
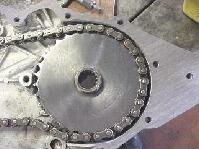 |
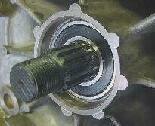 |
今回、両側ゴムシールドタイプのベアリングを、
グリス給油側のみ外して使用します。
シールドベアリングはキビシイ環境では、放熱に問題が有って、
完全に閉じてしまうと、耐久性が落ちる場合があります。
今回はチェーンオイルの侵入を2重に避ける為、
片側シールドにしました。
|
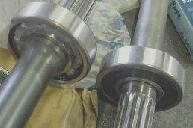 |
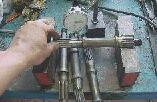 |
このシャフトは、構造上“片持ち”ですので、縁石に乗り上げた程度で、簡単に曲がってしまいます。
組み付け前に“シャフトの振れ”要点検!
リヤホイールがウネウネと?廻るS600をたまに見かけます!
|
どんなにがんばっても新品・純正部品にはかないません!(今回一本しかありませんでした↓)
|
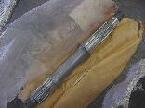 |
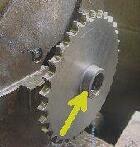 |
リヤスプロケットのこの部分は、オイルシール接触面ですが、
理由は解りませんが、溶接のスパッツが残ってたり、
不自然な、痕跡があったり・・・・
妙に?荒れている事が多々あります。(研磨して修正します。)
|
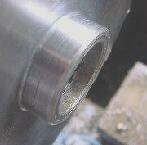 |
この部分のオイルシールはスズキ純正部品を使用。
サイズと材質に問題が無ければ、
旧車修理にメーカーの垣根は有りません!
(規格品には無い特殊サイズ!・・・S600のシールは殆ど規格外!)
|
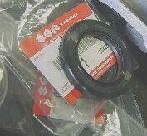 |
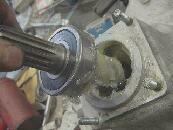 |
このリヤシャフト部分はグリス給油ですが、諸事情に拠り、オイル侵入が多々あります。
ブレーキ側は、Oリングとオイルシールでブロックされていますが、
バックプレート裏や、ドラムの中に滲み出る事あります。(旧いからしょうがないのも事実ですが!)
この部分も、片シールドでベアリング使用しました。
|
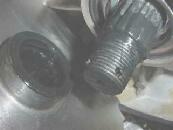 |
セレーション部分を介してのオイル漏れ対策に、液体P/Kを塗布して締め付けます。
S600は各箇所にOリングを入れて、くどい程?対策をしていますが、
オイルの浸透は容赦?ありません!(ハブ側も実施)
この位置場合、ワッシャー等で、ほぼ仕切られた環境になります。
ミッション用液体P/Kは乾燥が遅く、今回この場所は、エンジン用を使用します。
来週走るのです!・・・公道二百 キロ以上走行!
|
今回の作業に際して、チェーンの交換を検討しましたが、同一規格・強度では、市場に存在しません。
チェーンメーカーに依頼した、「新規作製見積書」は、2本で¥40万弱!
今回、6本の中古チェーンから選択する事に妥協しました。
|
一本づつ仮組して、チェーンアジャスターの右映像の数値を比較します。
ついでに伸びの均一性も点検!
更に横方向のクタビレ具合?を計測します。
|
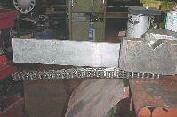 |
|
|
|
数値を成績表に付けて立候補者?決定!
機械部品は、成績表が全て!の キビシ〜イ・学歴社会!?
ドロップアウト!したい?気持ちになります!
|
|
|
リヤホーシング両端の映像。
オイルシールはホンダの2輪車
中央の保持用Oリングはカワサキ純正部品
ケースのスラスト調整シムは日産純正
今回3社・合同作戦 にしました。
|
このスラストの調整は、フレームにサポートを組み付けてから、
車上で実施した方が安全策です。事情はイマイチ解らない↓のですが、
修理書の様に車両から降ろした状態で基準値に調整すると、
フレームへのサポート取り付けが強引になり精神的に問題?があります。
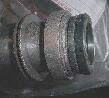 |
厚いシム(パーツリストに載っていない!)
は多種類が入れてあり、どれが正しいのか不明です。
(1,50.1,85.2,45mm)
(調整用の0,2 0,1mmは正解?)
今回は日産純正部品を選択使用しました。
(左映像はすべてホンダ純正品)
|
サス関連作業でシックネスゲージ・マイクロメーターを使う!
・・さすがHONDA S600!(少し頭がクラクラ・・!)
|
|
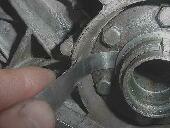 |
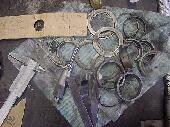 |
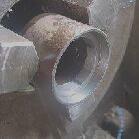 |
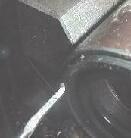 |
今回の代用品は、元々、
2サイクルのクランクシャフトシールです。
外嵌め込みを「内嵌め」に加工します。
最後にコンパウンドで最終研磨仕上げ!
|
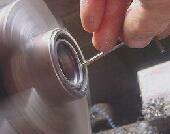 |
このスラスト調整の値と、オイルシールの転用を考慮して、
今回はチェーンケースP/Kの厚さを0,8mmから1,0mmに増厚して組み付けました。
|
ここで何時もの、気合の燃料切れ!です。
本日閉店です。
田舎の気合は・・弱いし、疲れやすいし、すぐ眠くなる・・そして視力が落ちる?!
その上に航続距離が少ない!
|
 |
|
ここまで、下手間作業が済めば、作業に勢いが・・・!!!
誰だって、どんな職業だって、「手間をかけた仕事」の結果を早急に確認したい気持ちは同じ!
|
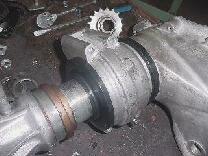 |
奇跡的偶然で?全部揃った純正部品のシール・ダストカバー類を組付。
アルミ肌を磨くのは手間が掛るので嫌い!ですし、
「職業柄、バフ掛け・アルミ肌は作業時気を使う!」なんて適当な?理由から
「そこそこクタビレタ感じ」を残す程度に洗浄。(悶々?)
以前に書いたアルミ鋳型の荒れやヒビに対して、実は大部分が鋳型表層部分が、
オイル漏れを防いでいる事実も、表面磨き等の行為の自粛要因?
(面倒くさい!・・・が本心?)
|
修理業を永くやっていると、美的感覚が歪んできて “キラキラ・アルミ肌” より、
新品シール類の “キラッと黒光り” が妙にウレシクて、妙にニヤついてしまう!(ヘンな?萌え萌え?)
薄汚れたアルミ表面さえ、ワビ・サビの世界!・・なんてズバリ!変人嗜好?しかも、ど真ん中 Strike!
|
すべてのシールが新品になった上に、
手羽先肩のチューブ部分を磨耗の少ない物に交換した為、
車両に組み付け後、グリスアップした際にインナー側のシールが、
グリス注入機材の圧力に負けて抜けてしまいました。
当然と言えば当然ですが、27年前に同じ事をした過去?を思い出し、苦笑いです!
車両上で組み付けるには、グリスの圧力を抜く為ニップルを外して実施。
|
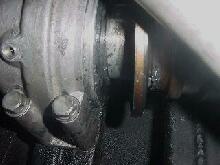 |
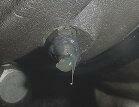 |
使用グリスはモリブデン含有の物(真っ黒グリス)をなるべく避けます。
すべての含有グリスがどうか?は不明ですが、
旧い車に使われているゴム類に膨脹性がある為です。
ブヨブヨになって溶けて崩れる!
(なんでもモリブデンを均等に拡散させる溶剤に問題があるそうです。)
|
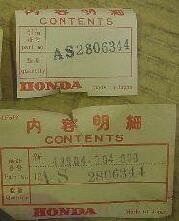 |
デフの頭部分を上下に挟んで固定するこのゴムですが、
かなり製作年度が旧い物で、旧表示の部番が列記されていて、
更に旧品番のラベルが添付してあります。
|
このS6が入庫しなければ、多分当工場の隅っこで・・
朽ち果てる運命?
数十年ぶりに、「本来の使用目的に復権」!
|
|
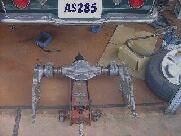 |
リフトに上げて作業すれば楽だし、作業効率も良いのですが、
どうしても長期化する運命を背負って?地ベタを這いずり回って作業!
これが何故か・・・懐かしい気分!
|
黄色↓のガスケットを忘れずに?貼り付けて組み付けます。
(本来の純正部品はアルミ板製ですが、G/K厚を換えるので、・・・。)
私だけの特異な傾向かも知れませんが、
全部組み付け後、組み付けを忘れた事・・を・・思い出します。↓↓
|
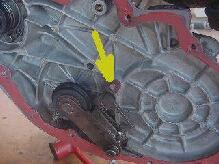 |
この時点で必ず、半割りの手羽先を上下に動かして、先のスラスト調整の具合を確認します。
数十年の酷使による結果か、元々設定に問題が有るのか、サポート部分の接触圧に問題発生!の場合があります。
樹脂円周上のひび割れ・・・
コレもひょっとしたらこの為?
|
|
当然、ですが逆に過大なガタが有る場合は、
耐久性・走行フィーリングに問題あり!
|
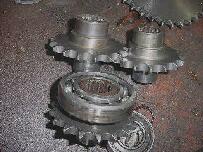 |
前側のスプロケットベアリングは要注意です。(殆どの物が何かしらの損傷アリ!)
ケース内の環境が異物や水分混入を受けやすいのか、ガタ有り!・・は必然?ですが、
一度固着後、ベアリング外側が共回りして、アルミケースを痛めている物もあります。
(この場合、ケース交換?・・大泣・涙!)
フラフラの?リヤシャフトを支える為か、内外共に結構強い勘合です。
このベアリングは規格品で安価(¥1500程度)ですので、
分解時は迷わず?交換した方が結局安全・安価です。
|
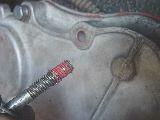 |
先のパンク修理の結果を考慮し、
雌ネジ部分を脱脂洗浄後、液体パッキンを塗布して組付。
|
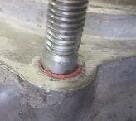 |
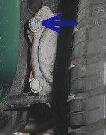 |
青い↓部分のボルト穴は深いカラーがあり、
有効なネジ長が、かなり短い!ので、長い物と交換します。
(ボルトの頭が12mmになってしまいますが・・・。)
|
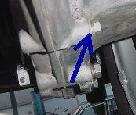 |
この時点で、以前よりオーナーが気にしていた、マフラー内部のカラカラ音を修理します。
(某オークションで程度の良いサイレンサーを購入しましたが、コレも、カラカラ・・カラカラ・・・)
|
|
当然?二十年来の友・旧式プラズマカッターの出番です。
切った後の歪みが殆ど無くて、しかも切断幅が1mm以下!
後の溶接が楽で綺麗に出来る!
(切断能力の大きい物は内部構成部品を切ってしまう!ので要注意!)
|
|
|
内部の消音材や、パンチング板を 出来るだけ 無傷で取り出す!為に
サイレンサー部分の縁、ギリギリを切り込みます。
右のパンチング部の前側部分を意識して?可能な限り、ギリギリ・・で!
|
|
|
パンチングの点付け溶接を最小限切断、各部を探検?します。
昭和60年頃の補給部品でしたら、黄色↓部分の
溶接不良か未溶接!・・・が殆どですが、
今回は新物?ステンレスナットを発掘 しました! ⇒
|
|
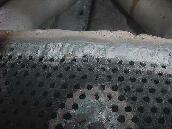 |
パンチングの前後をクソ丁寧に?溶接します。
この部分を手を抜かずに連続的に溶接できると
後で表面の板の溶接が思いのほか楽に?なります。
パンチングの歪みを木ネジ等で引っ張って修正します。 ⇒
この部分の出っ張りをサンダー等で平坦に削り、最終フタ閉じ作業です。
|
|
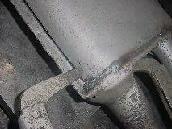 |
隙間を出来るだけ小さく均一にすると、溶接が上品に?仕上がります!
|
|
 |
美容整形後、手術?終了!
|
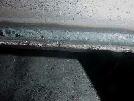 |
年式違いで、サイレンサーブラケットが取り付け穴届きません!
厚手のアルミスペーサーとベークライトでしのぎ?ます。
オークション等の “インターネット部品調達” は、
顔を合わせた訳でもないし、名前さえほとんど覚えていません。
(1〜2人、知人を介すると繋がってしまう恐ろしさも苦笑)
・・が・・なぜこの部品が現在まで保管されていたか?
・・は単純に金銭の為ではないと思います。
(保管のコスト計算したらたとえ、多少高額になっても・・・。)
私も大多数の物を売却し生活資金化(涙)しましたが、
“それぞれ、S600の為に保管していた部品”だと思います。
西の方の田舎?を走っています!
ありがとうございました。
|
|
本日閉店です。
田舎の気合は弱いし、疲れやすいし、すぐ眠くなる。そして視力が落ちる?!
その上に航続距離が少ない!その上、感傷的?
|
 |
|
幾多の苦境を乗り越え(笑)手羽先本体を組上ましたが、
ここだけ直せばOK!・・・なんて事、当然の様に! 40年の歳月と、その整備暦が許しません!
今回オーナーより、・・・以下・3点の修理依頼を受けています。
1)「フワついた感じ」 2)「効きが悪い」更に 3)「ぺタルに振動が伝わると同時にヘンな音が出る」
手羽先修理の際に後輪ブレーキ部分を分解するのでこの際に一気に?作業実施。
どんな車でもブレーキは消耗品の代表的部位ですが
それは、ライニングだけに留まらず、動く部分全域に及び、
使い込まれた車には各部にかなりの磨耗を伴います。
ましてや・・・約40年!
|
|
更に追い討ちをかける?様に、この頃のホンダ車は、
右側のリップが尖ったタイプです。
先端がハナマル状態?に変形するケースが多く、速めの定期交換が安全策です。
|
最近の車両は左のカップ様に
この対策と接触面圧を均一にする為に、
接触部分が丸い三角状になっています。
|
リバースタイプって名前で、トヨタ系列・ブレーキメーカーの十八番!だった様な・・。
|
|
不確かな記憶ですが、ホンダ純正部品では、(昭和60年辺りから?)ピストンセットで供給されていて、
ホイールシリンダカップのみは、入荷しなかったのですが、ネット上では比較的安価で入手可能です。
セイケン・クラッシック(社外品ブレーキ部品メーカー)でもラインナップがあります。
リバースタイプのS600用・補給品カップ(フロント用)も存在する用です。
(非純正か純正か?未確認です!)
|
この車両は今回当工場ではブレーキ分解の実施履歴が無いので、
とりあえず、マスターシリンダーと、前後のホイールシリンダーの内壁のコンデションを点検後、カップを交換します。
|
この車両はブレーキシリンダ各部は非常に良いコンディションでした。
すべてのアルミ部分に腐食や損傷が診られません。
当時のアルミ材質があまり良くない様で、珍しいケースです。
「ブレーキは重要な部分だから・・・!」前・オーナーこだわり部分かも?
|
後輪・黄丸部分はサイドブレーキの動作部分ですが、下映像のようにエグれて、
サイドブレーキが、効かない事があります。(溶肉盛り後、修正して再使用します。)
更にS8の場合、ライニングが2種類あって、穴の幅が異なり
品番を間違えると、全くサイドブレーキが効きません!
|
|
|
整備業界人なら、お気付きの事と思いますが、
つい最近のActyや、Todayでも同様のケースがあります。
車検毎の給油で殆ど回避可能です!
|
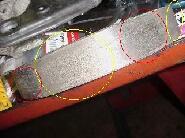 |
1)2)3)すべての症状の原因はライニングでした。
前オーナーが交換時、表面を削った折に、不均一になり、
異音や、異常を感じる原因になった様です。
|
ブレーキライニングの加工業者さんに持ち込めば、
特殊な研磨器具で各ドラムに合わせてくれますが、
今回は、「始め人間ゴン!的作業?」で手作業で当たりを診ながら実施!
|
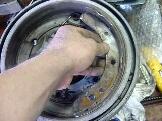 |
|
ライニングの汚れ?を診ながら少しずつ修正しますが、
作業者の性格と異なり?かなり根気を要する!仕事で、
4枚実施すると、何時もどおり?歯が浮いてきました!
|
|
ブレーキぺタル上部のマスターシリンダーを押す穴が
楕円になっている事がよくあります。あまり大きくなると、
ブレーキペダルを踏み抜いてしまう可能性アリ!
(実際はロッド部に引っかかる様ですが・・危!)
冷汗的な体験(↓)を避けるには?要整備部分です。
|
|
大きくなった穴をTIG溶接で、気泡を噛まない要に注意しながら穴埋めしてから、
再度既定のサイズ穴にドリル加工します。
(この際、マスターシリンダー側のピンも同時交換します。)
|
手羽先修理作業中に
山積みになった部品 を整理。
|
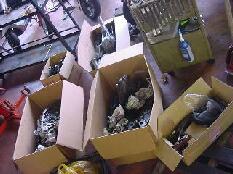 |
箱詰め後、オーナーに返却します。
|
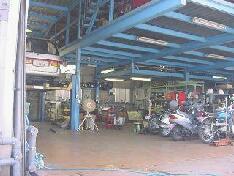 |
あふれた中古部品が無くなり、
工場内も、作業台の上も・・・
(本来バイクリフト!)
平穏な初秋の田舎工場?
|
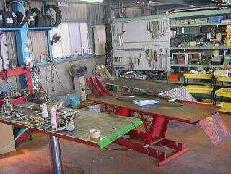 |
夜半にオーナー来店。
|
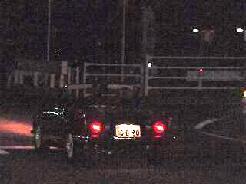 |
ホンダS600 秋風の鈴鹿に向けて発進!
当工場も、やっと「秋のK&K24戦」の準備作業が出来そうです! 06’SpecR発進!
|
・・・・のつもりが・・・鈴鹿のイベントまで 僅か3週間を残して、とんでもない重大なトラブル発生!
・・・・!!!(大泣・涙X100 + ↓X100!)
|
|